1. Machinable CMCs | 2. CFRP Dampers |
[I] MACHINABLE CONTINUOUS FIBER CMCs FOR HEAT-RESISTANT USES
Shonan-AML group develops and manufactures continuous-fiber reinforced ceramic composites(CMC) for applications requiring resistance to high temperatures (exposure to temperatures above 1200℃) with excellent fracture toughness in lightweight. These heat-resistant composites are manufactured by our cost-effective unique technologies and do not use complex processes and thus cost-effective, in comparison to conventional ceramic matrix composite such as chemical vapor infiltration (CVI). The new ceramic composite materials retain excellent mechanical properties as well as high fracture toughness at temperatures for which CFRP cannot even be considered. The Most surprising advantage of our CMC materials is that it exhibits excellent machinabilities (drilling, cutting, grooving and so on) unlike the conventional brittle ceramics.
The promising markets being considered for our CMCs are aerospace, automotive, marine, engines, tribological, structural, and energy related. Some of them are rocket nozzles, exhaust pipes, heat exchangers, hot-gas filtration devices, combustion liners, shrouds for gas turbine engines, furnace pipe hangers, sand blasting nozzles, among many others.
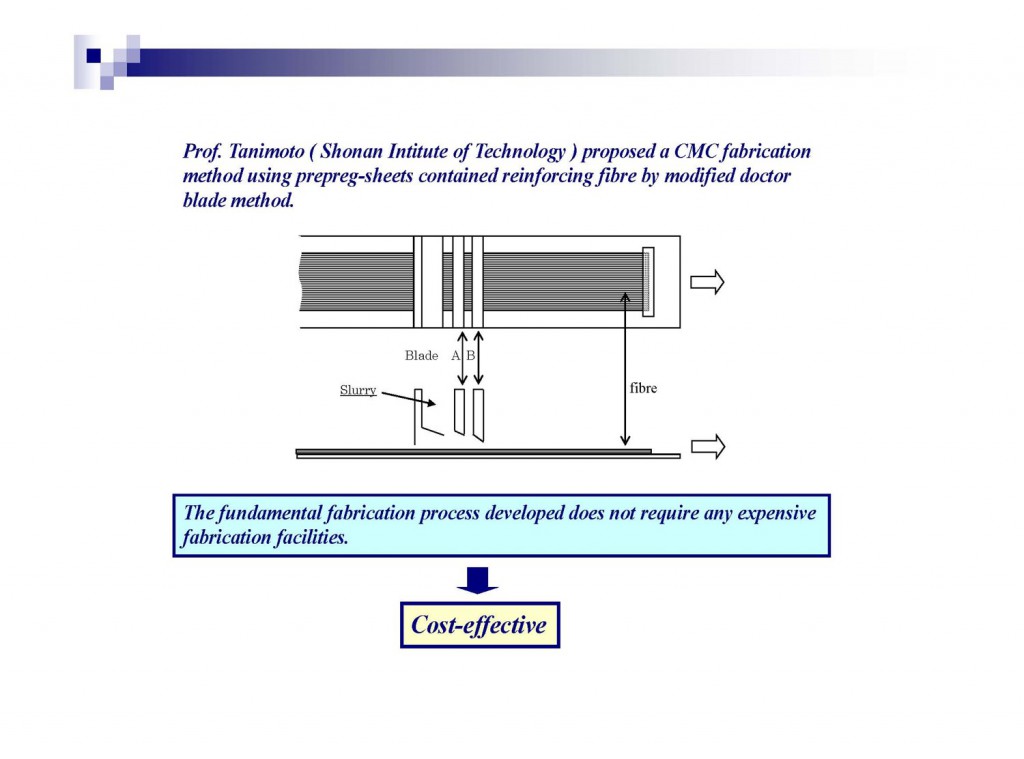
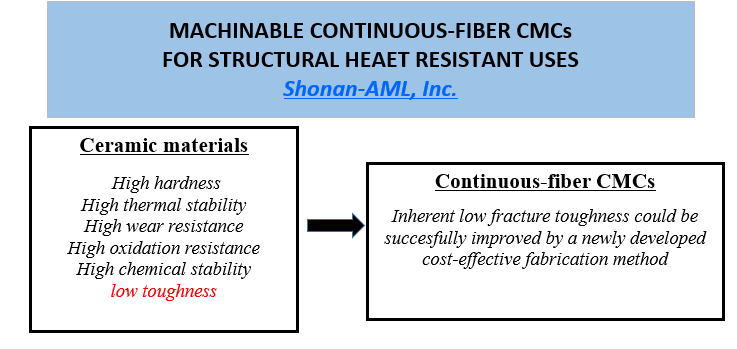

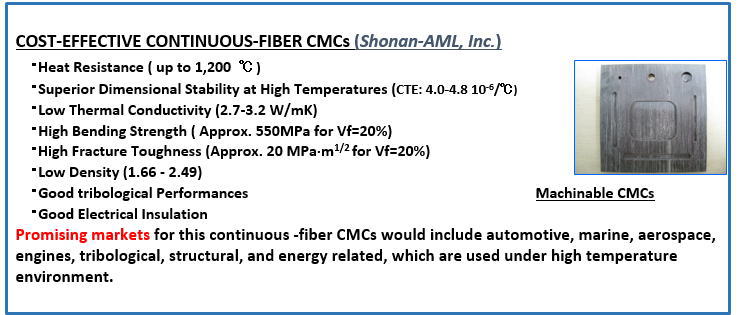
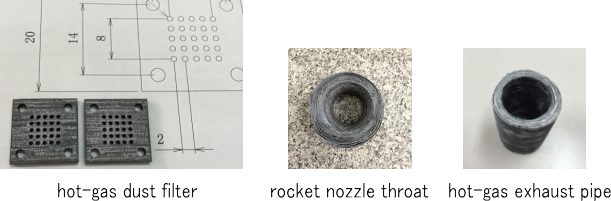
[II] A Vibration Damping CFRP Laminate Technology for Application to Large Light-weight Structures
Background
Although carbon-fiber reinforced plastics (CFRPs) have high stiffness and low density, these materials are considered to be unsuitable for large light-weight structures that produce vibrations under operating conditions. Two specific examples of such structures are “Wind Energy Blades” and “Robotic Arms for Industrial LCD Conveyor Systems,” which require high vibration damping capability in addition to high strength/stiffness and low density. Generally speaking, it is believed that materials with high stiffness belong to the low vibration category. In other words, Stiffness and vibration damping are incompatible with each other. In this sense, CFRPs inherently possess low vibration damping performance, since the loss factor of conventional CFRPs is generally measured to be approximately 0.001-0.005. In actual applications to large light-weight structures, one-order higher loss factor of 0.01, for instance, would be required, and thus a great demand has emerged for advanced CFRP materials with highly improved vibration damping.
Proposed Solution for Resolving the Vibration Problem
Dr. Toshio Tanimoto, Founder and President of Shonan-AML, Inc. Japan, has long been investigating two particular methods for improving the vibration damping of CFRP materials: (1) interleaving of viscoelastic thermoplastic films and (2) resistively shunted, surface-bonded piezoelectric ceramics.? Dr. Tanimoto also developed an original method to enhance vibration damping of CFRP laminates via dispersed piezo-ceramics (PZT) particle interlayers. Please see a movie which compares the vibration damping behavior between conventional CFRP laminate (right) and our CFRP laminate damper (left).
Importance, Uniqueness, Technical Merit, and Potential Application of The Proposed Damping Method
The uniqueness of this damping method is that the different damping methods can be jointly used to improve the damping of CFRP structures, that is, combination of interleaves of viscoelastic thermoplastic films and interlayer of dispersed PZT particles between composite plies. They only differ in an existence of thermoplastic interleaves and a piezo-ceramic interlayer. In addition, the newly developed passive damping method does not require any electric circuits or electronic processing.
There will be many potential industrial applications for the developed CFRP damping materials. For instance, low vibration spacecraft structures, car suspension, robotic arms, wind energy blades, and other CFRP large structures which require high vibration damping capability in addition to high strength/stiffness in low density.
These original damping technologies for CFRP laminates were patented by Dr. Tanimoto, Emeritus Professor of the Shonan Institute of Technology (Founder and President of Shonan-AML, Inc.), in 2003 in Japan, together with international patents for USA and Germany held in 2006, allowing for easy access to the technology.
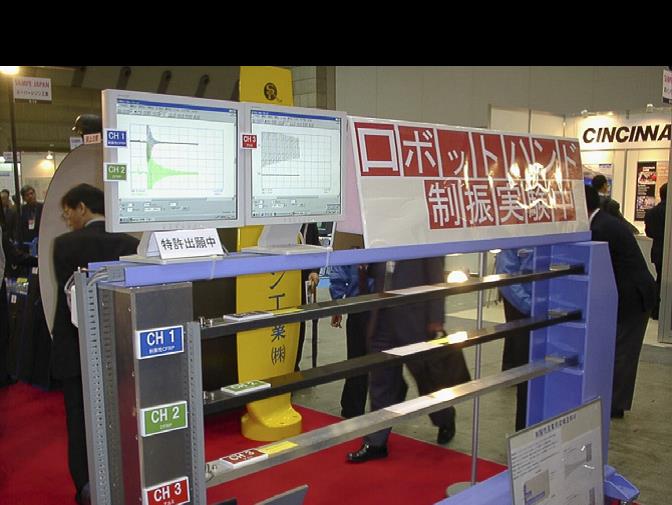
Vibration damping measurements for damping CFRP arm (CH1), conventional CFRP arm (CH 2) and aluminum arm (CH 3).